Munich, Germany, October 29th, 2024. With daily production of around 1,000 vehicles and almost 7,000 employees, the historic main site in Munich is an indispensable part of BMW’s global production network. Production of the new vehicle architecture, New Class, which uses only electric drive systems, will begin here from 2026. The automaker is investing 650 million euros in a new vehicle assembly facility, including logistics areas and body manufacture. The extensive conversion work is being carried out while operations remain ongoing. Drees & Sommer SE specializes in construction and real estate consulting. The company’s interdisciplinary team supports the large-scale project with expertise in the areas of project steering, construction management and building information modeling (BIM). Together with BMW Group, PORR AG and PDE, Drees & Sommer is focusing on an innovative collaboration method.
Maximilian Lammel, senior team head at Drees & Sommer comments: “The biggest construction challenge is the tight schedule. We started the demolition work in April 2023 – the new vehicles must roll off the production line in November 2026. During this period, the construction work must not interfere with ongoing vehicle production. For this to work, an efficient construction workflow is crucial. This requires that everyone involved in the project pulls together and communicates with each other on equal terms.“
The New Delivery Model Is Based on Partnering.
For this reason, the project uses the partnering delivery method, also known as ‘general contracting in partnering’. Right from the beginning, client, planning company and construction firm interact as partners. In concrete terms this means that the teams of BMW Group, PORR AG and Drees & Sommer SE work together in each of the construction stages and mutually support each other in all phases of the project.
“Mutual and joint responsibility improves the communication between stakeholders and enhances the quality of construction projects,“ says Maximilian Lammel. “In conventional delivery methods there are many sub-areas of responsibility, with communication being conducted via several interfaces. This often leads to misunderstandings and hampers the flow of information, especially in large-scale projects. The consequences could be disastrous. Thanks to our partnering model we are able to create a transparent and cooperative working environment. The type of collaboration used in this project promotes mutual understanding and shared responsibility for its success,” he continues.
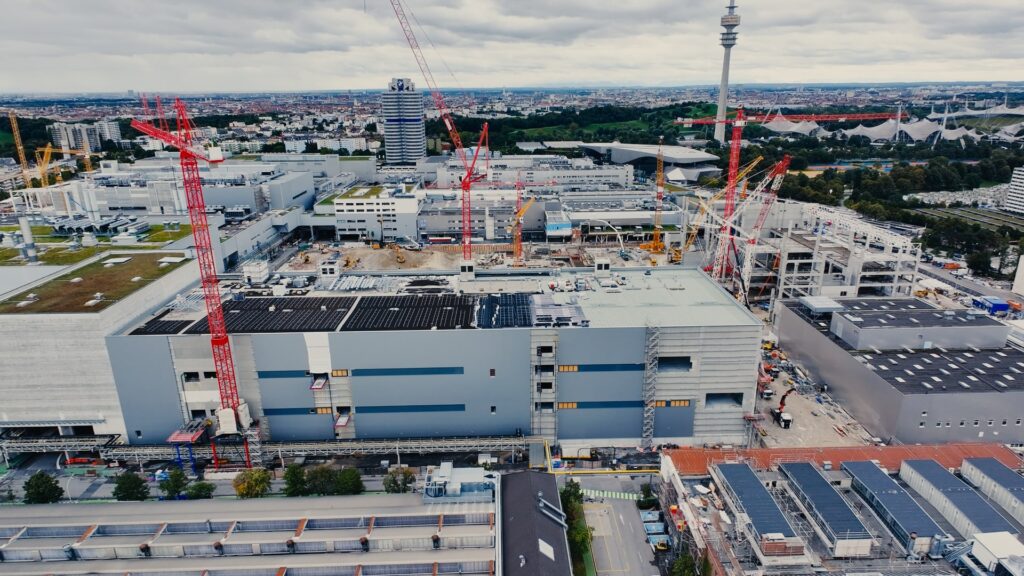
From the Automobile to the Construction Site: Lean Principles Accelerate the Building Process.
To ensure that the construction project is completed within the required timeframe, Maximilian Lammel and his team are applying the principles of lean management. The method is borrowed from the automotive industry: automakers know exactly when which vehicle with which equipment will roll off the production line. If there is any fault in the precisely timed production process, the response is immediate. The cause of the fault is identified and fixed as quickly as possible. On a conventional building site, on the other hand, defects often go unnoticed for a long time – sometimes so long that, at some point, all work comes to a standstill.
“The lean construction management method we have developed transfers the automotive industry approach to construction projects. The planning and implementation process is set up as efficiently and in as much detail as necessary, so that all trades work together to the best possible effect,“ explains Florian Langlotz, Partner at Drees & Sommer Group and responsible for the Automotive division.
The first step was therefore to initiate communication between everyone involved. The focus was on optimizing the scheduling of the building site and the overall process, aiming at a consistent implementation plan. A clear definition emerged at the end of this planning, indicating when which employees, machines and construction materials were needed at which location and at what time – without idle time or delays due to a lack of materials or plans, and without the various trades getting in each other’s way while working. The result was that the planning grid for the shell of a new assembly hall was completed in just ten days.
A Digital Twin Ensures a Maximum of Planning Security.
These minimal timeframes are made possible not only by the efficient construction work. “To avoid any nasty surprises on the building site, we use virtual planning,“ says Drees & Sommer’s senior team head Simon Rogalski, and explains: “Each building is initially planned in the form of a digital twin, which brings together all the relevant data. In this method, the construction planners not only describe the geometry of the new halls. The model can be enhanced with different kinds of data on the materials used, their cost and service life, as well as sound insulation and fire safety properties.“
This type of detailed planning does increase the planning effort at the start, but pays off over the course of the project. All parties involved in planning and construction use the same model. So, all information is immediately available. If the designs no longer match, for example, the conflicts are directly visible in the digital twin. Errors are not left unnoticed until the construction process, where they would then lead to expensive delays. Hence, virtual planning ensures maximum planning security and a close collaboration of all stakeholders.
The new halls should be up and running in two years. Auto production will then start at full speed on the main site in Munich. One year later, the Munich plant will be the first BMW Group production site in the world to manufacture only fully electric vehicles.
About Drees & Sommer
Uniting opposites to create a world we want to live in
Drees & Sommer is a partner-managed, global consulting company providing a single source of consultation and implementation services for the real estate, infrastructure and industrial markets. The company delivers sustainable, innovative, and economically viable solutions that meet each client’s unique needs. Founded in 1970 and long recognized as a pioneer in driving sustainability and digitization, today Drees & Sommer employs more than 6,000 people at 63 offices. The company’s interdisciplinary teams are involved in around 6,500 projects worldwide, working to create a livable future and unite concepts which can at face value appear to be opposites: tradition and future, economy and ecology, analog and digital, efficiency and well-being. As ‘intrapreneurs’, the Drees & Sommer Partners are personally responsible for managing the company.
Zdroj: Drees & Sommer